Explore My Work
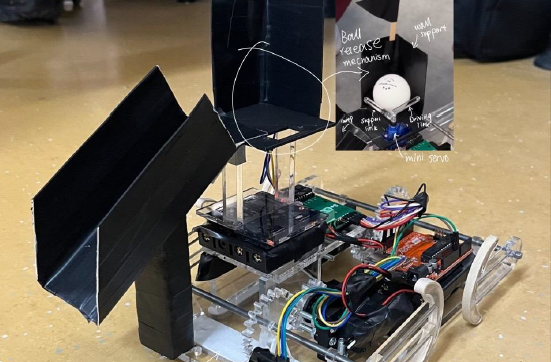
[1]
Ping Pong Robot Challenge
The goal of this project is to successfully design and fabricate a robot with the goal of moving forward, stopping, launching a ball into a goal, and then moving back to its initial position to reset and repeat. The main design constraint for this project was our main "wheels" driving the robot cannot be a round wheel.
Project Takeaways
-
Creating and constraining assemblies in Autodesk Inventor
-
Integrating electrical and mechanical components
-
Problem solving
-
Design for testing
From this project I learned alot about team collaboration and system design. Looking back on this projet, with better time management on my end and more team communication and time dedication, we could have evaded a lot of problems we faced during testing.
Something big that we didn't really account for was how we would access the electrical components during testing in case anything failed. Due to this oversight we faced a couple challenges when our robot was put to the test as it was a struggle to reposition our components.
There were a couple things that I thought were pretty cool about our design. We added felt pads at the bottom as a shock obsorber so when the legs moved and the robot was momentarily on the ground between movements, there was no damage to the base of the robot. We also added rubber bands on the bottom of the legs to improve traction and prevent slip. We also used lightweight materials such as foam and carboard to build a platform for our ball-release mechanism withouth adding weight.
Overall this was a great learning experience and I had a lot of fun working on this project with my team!
Design Process
For this project, we decided to focus on functionality as our main criteria. We took all the ideas that we came up during our initial brainstorming sessions and evaluated them one by one. We evaluated the uncertainties and possible problems that would be associated with each one and developed our ideas so that with all the uncertainties, our ideas would be guaranteed to work. From there, we were able to evaluate other criteria and decide our action plan from there. Also, as a group preference we decided to focus on creativity as a secondary objective.
Based on our decision matrix, the chosen design for the transmission is a four-wheel drive transmission as it is
the most efficient way to overcome all obstacles on the way. This propulsion allows us to move backwards along the same axis after releasing the ball. This way, we avoid any uncertainties associated with turning, ensuring that the robot returns back to its initial position, and it will be ready to go for the next cycle.
After weeks of design and last-minute problem solving, we were able to come up with our final design and although we faced some chellenges with broken motor frames and an extremely heavy body (laser-cut acrylic) we had a great time working on this project and were pleased that our robot performed well and our ball release mechanism was pretty solid as well!

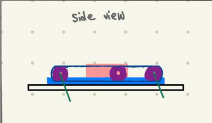

Figures 1-3: My Proposed Transmission



